What does it mean to be a key OEM supplier?
- Digital Factory
- Article
New car models are coming onto the market every day. And each new model is accompanied by a number of variants that we as customers can choose from. The effects are obvious. The number of Just in Sequence (JIS) suppliers – those delivering parts in sequence straight to the assembly lines of automotive manufacturers (OEMs) – is on the rise. “In sequence” means that products come prepared in the same sequence as will be used for assembly on the line. Why is this done, and what does a supplier need to do to satisfy customers in the tough automotive environment while also keeping full control over the fulfilment of the contracts?
Why are parts delivered in sequence?
The answer is simple. It saves automakers’ money – and space in their halls. Because the parts are readied in the correct sequence, they need less handling, preparation and repacking. Besides the labour savings, a large amount of space is also conserved, both in storage and right in the assembly area next to the line. This leads to one simple rule: if a part requires a stock of one or more pallets and comes in multiple variants, JIS delivery is a sensible choice.
It’s not easy being a JIS supplier
The market today is very unstable. Things that were standard in the past no longer apply at all. Suppliers for automakers must have everything under control nonstop and in time and handle multiple tasks at once. They must achieve and maintain high part quality so as to pass customer audits with zero errors or objections and support complex processes. They must be able to show proof when call-offs have been changed outside of a contract, or a part or module has been produced but not yet invoiced. Whenever there is a call-off for a new module variant, or a part in a call-off has a far more complex manufacturing process than usual, or special components are running low, they should be informed of this. They should ensure that assembly workers on the line make zero mistakes and comply with the manufacturing procedure, including torques, tool angles and tightening speeds.
At the same time, they want to reduce manufacturing costs and keep a project profitable throughout the entire cycle. They also aren’t allowed to stop the automaker’s line. The issues and questions are many. Can an information system help with it all? And what should it do?
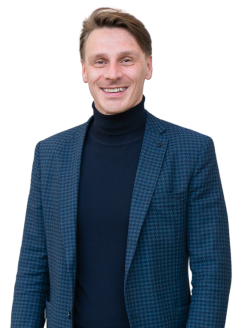
“One of our customers is the automaker MAN, for which we manufacture complete pedal assemblies. We supply these in different variants, and before sending them off, we palletize them in a precisely defined pearl chain sequencing order (Just in Sequence), which corresponds to the vehicles’ sequencing on the production line. Through the automation of processes and the use of robots, lift systems and conveyors, we have eliminated the human factor and the risk of confusing one part for another to the maximum extent possible. I perceive how this successful pilot project is fundamental for us and is a gateway to similar applications for the other passenger and utility automobile manufacturers in our portfolio.”
Václav Juříček
CTO, member of the board, BRANO GROUP
The 10 roles to keep in mind
The information system used by a JIS supplier must meet a number of requirements. Every company has some sort of system, but the goal should be overall digitalised, automated processes requiring no human intervention. Here are 10 important characteristics of a system that will lead to full digitalisation.
- It accepts and processes EDI call-offs – it lists what parts, in which specification and in which order are to be delivered to the automaker.
- It draws up a production plan for assembly that evaluates what should be manufactured, in what order, on what lines, using what components and production parameters.
- It manages the transport of all components and parts to the work area in kits, kanbans or in sequence, as assembly requires.
- It guides operators so as to eliminate mistakes.
- It transmits programming to machines or tools (e.g. screwdrivers) to ensure compliance for torques, pressures and times.
- It assesses whether production was in line with procedures and all parameter tolerances were met, stores all the data and remembers the entire biography of every product.
- It plans and synchronises all pre-production and pre-assembly steps so that batch production maintains the correct takt and no parts are missing.
- It generates requirements for all suppliers so that they know what and when to ship, everything fits in the warehouse and, once again, no parts are missing.
- Besides workers, operators and handling crews, it also digitally controls all the automated machines and robots.
- It collects data for detailed analysis and future optimisation.
What’s the road from here to there?
Factory digitalisation is always a thoroughly specific task. Therefore, the solution used must be configurable and flexible enough to allow maximum adaptation to a given factory’s requirements – both current and, above all, future ones. The road to success lies in combining and integrating multiple solutions into one whole: MOM (Manufacturing Operations Management). It factors in production (MES), quality (QMS), logistics (WMS), maintenance (MMS) and planning (APS) – in short, processes throughout the factory and its manufacturing sites. It also takes care of electronic communication with suppliers and customers (JIS/JIT and EDI). All the areas work with the latest data, and detailed traceability can be achieved without the need to collect and connect information from multiple sources; it’s all in one place.
Share article
Top stories from logistics, production and IT.
Subscribe to Aimtec Insights
By registering, you agree to the processing of your personal data by Aimtec as described in the Privacy policy.
Get top stories and articles
from Logistics, Production and IT.
Subscribe to Aimtec Insights
By registering, you agree to the processing of your personal data by Aimtec as described in the Privacy policy.