Simulation Tools: The key to efficient process planning in manufacturing and logistics
- Trends
- Article
How can you ensure effective evaluation during the planning processes in a project’s opening phases? Can advanced add-ons like virtual reality and artificial intelligence tools make simulation models more effective? And how necessary are comprehensive simulations of production and logistics systems for proper estimation, process planning and better awareness? Tomáš Sauer, Global Competence Field Leader at FORVIA HELLA, answered all this for us at the Trends in Automotive Logistics (TAL) 2024 conference.
Even though few will admit it in formal conversation, for many of us our “dream job” isn’t work itself, but rather simulated work. Tomáš Sauer opened his talk at TAL 2024 with this observation. While it’s just a bit of wit, it’s also a great fit for the topic of Sauer’s presentation. That’s because this FORVIA HELLA manager can rely on a tool whose precise purpose is the simulation of a variety of work-process models.
The birth of FlexSim
Overall, what made simulation tools necessary was the increased complexity of logistics: Excel tables no longer sufficed, and dynamic tools gradually began to replace them. Among the companies that felt this need was FORVIA HELLA, which chose the tool named FlexSim. In 2013, it purchased a license, and a year later it developed its own internal library, in which users have objects available for quick use. “Simulations then became a standard for both our divisions – electronics and lighting. No new projects may be started, and no new investments approved, unless the simulations have confirmed that the system will work as we imagined.
Preview of the FlexSim software
Around 2020 we implemented a superstructural solution, and then we appended process-planning tools, robotic simulations to give us more technical background, and also an extension to add features such as virtual reality and AI methods,” was Tomáš Sauer’s recapitulation of how the simulation tools at FORVIA HELLA have developed. He added, however, that they’re far from done and that the system will be enhanced with further innovations. At present, the corporate team behind FlexSim is providing this tool to over fifty factory-level users worldwide. “We provide not just support – in other words help with developing simulations – but also various training concepts, that is, every course from the basics to programming to advanced training,” Tomáš explained. One important part is the development of pilot projects, as well as methods, which the above-mentioned libraries are used for.
On the assembly line
Practical examples always provide the most convincing proof that a given solution works well. So how do things look when FlexSim is deployed into live operation? Its simulations typically deal with several crucial subjects. They include takt time, device count, buffer requirements, operator positioning, bottlenecks, NOK effects and various scenarios.
The benefit is that the simulation always takes into account the “safe minimum”, thus saving the costs that excess project capacities would generate.
Tomáš Sauer, Global Competence Field Leader, FORVIA HELLA
Sauer presented an anonymous client’s assembly line as a reference. “We started out with an interest in the time cycle, the optimum machine count and ‘what if’ scenarios,” Sauer said. To determine these values, Sauer’s team developed its own tools and calculations (for example in the case of “what if” scenarios, this is the incorporation of individual devices’ expected repair times). Each variant is projected into graphs and tables, thus creating a new version of the simulation. The benefit is that the simulation always takes into account the “safe minimum”, thus saving the costs that excess project capacities would generate. In this specific case the simulation took the form of a visualisation of an assembly line’s operation, including the movements of “live” operators around the machines. As a result, this was not a fully automated operation.
Deployment into logistics
In the case of a simulation in logistics, besides the basic requirement for a smooth flowing of logistics processes, there’s an emphasis on feeder positioning and on counts and arrangements for machines, i.e. for AGV vehicles and drivers, and an overview of storage spaces.
The example in question related to a European FORVIA HELLA factory, where the task was to deploy AGVs into an existing environment. “The supplier offered ten AGVs as the ideal solution. A FlexSim simulation was our only option for verifying this, and the answer popped out that five vehicles would be enough. So here we already achieved major savings,” Sauer said. However, this projection didn’t factor in overall mobility throughout the plant. “When we counted in all transport and the movement of people on this site, we realised five vehicles would not be enough. They’d be blocked here and about and wouldn’t keep up at hauling everything. Adding vehicles wasn’t the answer, as it just added blocked vehicles. We eventually reached a point where the simulation told us that the concept itself just couldn’t work,” Sauer described.
The simulation thus clearly showed that introducing AGVs into an existing narrow-aisle environment is not a good idea. The result was a solution comprising conveyor systems suspended under the ceiling, which was a concept confirmed both in simulations and later on in practice.
Superstructural solutions
As mentioned above, Sauer’s team is working on further add-ons for the FlexSim simulation tool. One of these is virtual reality. “To put it simply, virtual reality enables us to put on glasses and walk around the simulated environment. But we’ve developed additional tools that also enable interaction in the simulation, which can serve well as training for our operators,” Sauer added.
Assistance from artificial intelligence is demanded of almost every IT product these days, and this is no exception. “FlexSim specifically works with the method called ‘reinforcement learning’; this involves launching the model, teaching it and applying it using Python scripts. Here we tried the optimisation of production sequences and of routes for AGVs,” the presenter described. The use of the Nvidia Omniverse platform, which allows the streaming of 3D data into simulation software, is more a matter for the near future than today.
“I see some sense in the future connection of simulation software with material flow monitoring tools and with robotic simulations. Imagine a conveyor system; a pallet arrives at one end, at that moment I switch into the robotics software, where I’m running a real-world simulation of the trajectory, and a real-world simulation of the robot’s time cycle, and as soon as the pallet is loaded onto the AGV or the train, I switch back into the simulation tool.” With these words, Tomáš Sauer closed his speech at TAL 2024.
The benefits of simulations in planned processes are obvious, and they grow along with projects’ size and costs. They let firms correct and improve their plans – and also abandon them entirely if a simulation shows they are not viable. They can thus save companies large sums.
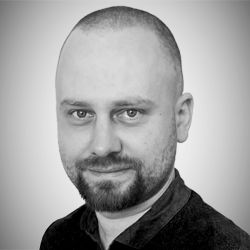
Tomáš Sauer
A graduate of Tomas Bata University in Zlín, Tomáš Sauer has been working at FORVIA HELLA for nine years. He is an industrial engineering specialist who leads a team focused on process innovations. In the Czech Republic specifically, there is a five-member team working mainly on simulations.
Share article
Top stories from logistics, production and IT.
Subscribe to Aimtec Insights
By registering, you agree to the processing of your personal data by Aimtec as described in the Privacy policy.
Get top stories and articles
from Logistics, Production and IT.
Subscribe to Aimtec Insights
By registering, you agree to the processing of your personal data by Aimtec as described in the Privacy policy.